A Concrete Solution For Accelerating Data Centre Development
- dcb1960
- 2 days ago
- 6 min read
FP McCann’s Operations & Commercial Manager, John Baker, explains why precast concrete is fast-emerging as a silver bullet for data centre developers as they seek to overcome the significant construction challenges facing the sector, and ensure the UK does not fall behind in the technology race.
The data centre sector is experiencing exponential growth globally as new technologies, increasingly driven by artificial intelligence and machine learning, demand a significant increase in capacity. Such is the pace of the development of these technologies that time is of the essence, given that a failure to meet demand for data centres urgently could hold back businesses and stifle the UK’s economic growth. The need to deliver data centres fast is recognised at government level too.
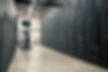
The Chancellor Rachel Reeves recently announced plans to tackle the “slow planning system” in the UK, which aims to ensure data centres are built faster to support AI-led innovation – another of the government’s economic priorities. Whilst the construction products sector may not be able to influence reform of the planning process, it does have a huge role to play in helping developers create data centres in the shortest possible timeframes without compromising performance and functionality objectives. And it is here where a building approach that has served us well for centuries is now supporting the development of our next generation technologies – precast concrete.
Why do we need data centres?
Data centres are critical to modern life functioning. They are buildings containing banks of computers which power everything from the internet, AI, cryptocurrency and streaming to our data storage cloud services, and were recently described as “the engines of modern life” by one UK government minister. There are an estimated 400 data centres in the UK, with global tech giants including Amazon, Microsoft and Google amongst those who have either already developed facilities or looking to do so. It is a sector experiencing significant growth with projections suggesting the market could grow at a rate of around 10% annually, with potential for even higher growth if the UK can increase data centre supply above its recent growth rate of 10-15% a year.
What makes constructing data centres uniquely challenging?
All commercial buildings have to be designed and built in line with the latest building regulations and sector-specific legislation that applies, but there is a combination of factors that make data centre construction unique. These primarily relate to power accessibility and supply, cooling, security, sustainability and accommodating the weight of the equipment and infrastructure, but there are others such as providing flexibility and adaptability of spaces and a shortage of skilled people to build them. Add in the need to build data centres rapidly and it is clear to see why precast concrete products offer significant advantages.

Benefits of precast concrete for data centres
Thermal mass to regulate internal temperatures - As a dense material, concrete provides a high level of thermal mass. This means it can absorb and store significant heat, helping to moderate temperature fluctuations within buildings to reduce energy consumption and deliver improved comfort. Given that data centres are designed to house equipment which generates potentially high temperatures during routine use, the building fabric’s ability to regulate internal conditions is an extremely important consideration. This is primarily because it reduces the risk of overheating, particularly during the summer months, thus lowering the demand for artificial cooling through air conditioning systems.
Optimisation for fast-track construction - Precast concrete was one of the original modern methods of construction (MMC), long before the term was coined. Hence why FP McCann undertakes numerous Design for Manufacture & Assembly (DfMA) projects across the UK and Ireland, including data centre construction.

Products are made in a factory environment, where quality consistency can be carefully maintained, and delivered to site for installation, a process that can complete projects 25% to 50% quicker than traditional building methods. Speed of construction can be maximised by choosing precast concrete solutions for key building elements like lift shafts and walling, as well as for the main structural framing. Standardised and customisable precast components also enhance the efficiency and scalability of data centres, and modular precast designs are beneficial in enabling the future expansion of data centres. In addition, choosing precast can also mean reduced disruption to the site and surrounding areas as fewer delivery vehicles may be needed to transport construction products to site. This is a sustainability benefit too.
Easing the skills shortage - Another benefit to precast products being made offsite, is that they can be assembled with relative ease on site. Using precast concrete instead of other approaches, such as brick and block or metal cladding and roofing, reduces the number of trades needed on site – really important given the national skills shortage affecting construction.
High security and fire safety - Given the critically important role data centres play in our national infrastructure, they are vulnerable to terrorist attacks. Hence why their design requires sandwich cladding from the ground to a height of 3.5m. Precast walling can be used here to provide a high strength solution which is robust to resist the impact of terror attacks. The strength of precast concrete can also help to protect the building from accidents occurring within the data centre.
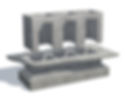
In particular, precast concrete walls can be specified to offer blast resistance to protect the structure, high value assets and people in the event of an explosion. Fire safety can be optimised too, not only to protect against fires resulting from terrorism but from fires that could originate from within the building.
This is a particularly important consideration for data centres given the presence of so much electrical equipment and extensive networked systems. Choosing precast concrete has benefits here because it offers a high level of resistance to fire compared to other materials.
And, for example, FP McCann can even cast conduits into the precast concrete floor and roof products to reduce reliance on plastic conduits, which are more vulnerable to fire. The performance of precast concrete in this respect means it is particularly suited to creating secure enclosures housing sensitive infrastructure, such as power and networking rooms.
To illustrate the depth of fire testing that has been undertaken on precast concrete products, FP McCann has conducted real life scenario fire tests in conjunction with Ulster University to document the robustness, sustainability and fire resisting qualities of precast concrete sandwich panels as a construction method.
During the tests, the PIR insulation core of the sandwich panels remained encased within the layers of the precast concrete. The outer concrete layers, due to their low thermal conductivity, protected the PIR insulation core from direct exposure to heat and flames.
Structural and load-bearing benefits to accommodate heavy loads - The strength of precast concrete is also more suitable for accommodating the weight of the technology packed into data centres. Choosing precast concrete flooring, such as beam and block or hollowcore planks, for example, are very effective at accommodating heavy equipment loads, raised access floors and cooling systems, amongst other objectives of a more structural nature.
Precast flooring panels can also span much further than many other materials which can mean fewer structural columns are needed. This increases the versatility of internal spaces so that can be reconfigured more easily throughout the operational life of the data centre. A sustainable material choice - The sustainability credentials of precast concrete also mean that developers can achieve strict targets relating to embodied carbon and whole life carbon emissions, including in line with globally recognised sustainable building standards such as BREEAM and LEED.
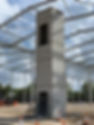
The processes used by FP McCann for manufacturing, for example, are designed to optimise resource and energy efficiency including through recovery and recycling initiatives. The result is a product with a very long lifespan that is manufactured in the most efficient way. In addition, FP McCann’s design team is accredited to BIM Level 2. By integrating BIM throughout the design and construction process, they can support carbon footprint analysis and material optimisation.
Precast concrete products for data centres - FP McCann’s range of precast concrete products is ideally suited to data centre construction because it covers all the main building elements to facilitate rapid, high quality construction. A full structural system can be provided, tailored to the requirements of the project, including elements such as precast staircores, lift shafts, stairs and landings, as well as hollowcore slabs, columns and ground beams. In addition, the FP McCann range also includes solutions for non-structural or façade elements. These include sprinkler tanks, for use internally or externally, dock levellers, substations for air cooled HV (high voltage) plant and numerous precast products to construct a full drainage system for the site.
How FP McCann supports data centre developers, engineers and architects - FP McCann’s in-house design team is highly experienced, skilled and resourced to add significant value throughout the design and construction of data centres. Key to this is the team’s BIM Level 2 compliance, which ensures efficient collaboration with architects, MEP engineers, and contractors.
This helps to reduce design clashes early in the process, prevent costly on-site issues, and enable data-driven decision-making for enhanced project accuracy and coordination. The team’s Tekla expertise enables them to create detailed 3D models of precast elements, such as walls, floors, and structural frames with ease. Not only does this provide automated fabrication drawings to streamline manufacturing and installation, but it also detects clashes and optimises coordination to ensure all elements fit precisely before production.
Finally, the wider FP McCann team is structured to provide end-to-end design and engineering support. This offers assistance from early concept design to installation, ensuring seamless project execution. For example, custom detailing can be developed for complex layouts and equipment-heavy zones, and real-time updates to models can be done to accommodate late-stage design changes. It all adds up to a more efficient construction process to enable the rapid delivery of data centres. www.fpmccann.co.uk.